A Goods Received Note (GRN), also known as a Goods Receipt Note, is an important document used in the supply chain and inventory management. It serves as a record of goods physically received by a business or organization from a supplier or vendor. The GRN is typically created after the delivery of goods and is an essential part of the procurement and inventory control process.
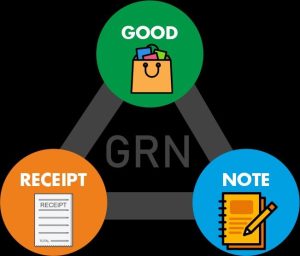
Uses of goods received note
A GRN acts as a confirmation mechanism for delivering goods for both parties. GRN is applicable in case of many situations:
- Record for the future: A record of goods received can be used as a reference for future cases such as resolving disputes or audit trails.
- Examining goods received: GRN helps validate the quantity and quality of goods received by the buyer. It helps to inform the supplier that the goods are of an acceptable standard.
- Inventory management: GRN assists in keeping track of inventory levels and thereby helps maintain accurate inventory levels.
- Assist in accounting: With the help of GRN, accountants can confirm inventory balances and update the stock ledger against purchase entries. This also helps in managing accounts payable. Items not received as per GRN can be subtracted, and the suppliers may pay the balance.
Format of goods received note
A Goods Received Note (GRN) typically follows a specific format to accurately record the receipt of goods from a supplier. Here is a simplified format of a GRN in human-written form:
[Your Company Letterhead]
Goods Received Note (GRN)
GRN Number: [Unique Identifier]
Date: [Date of Receipt]
Supplier: [Supplier’s Name]
Supplier’s Address: [Supplier’s Address]
Contact Information: [Supplier’s Contact Details]
Purchase Order (PO) Number: [If Applicable]
Invoice Number: [Supplier’s Invoice Number]
Received By: [Your Name]
Department: [Receiving Department]
Contact Information: [Your Contact Details]
Process to issue goods received note
A GRN helps improve efficiency in the delivery stage of the procurement process. The following process flow is followed:
- Receive invoices and purchase orders for the goods.
- Supervise unloading of goods at the location.
- Conduct physical verification of goods received to ensure quantity and quality of materials are as per the purchase order. Perform quality tests on a few materials.
- Inform the supplier in case of a shortfall in quantity or disputed goods.
- Once verified, the store’s department will issue copies of GRN instead of approved goods. The notes must be signed by the store’s department manager and verifier. A copy is given to the supplier to acknowledge receipt of goods. The other copies are sent to the relevant departments.
- On receipt of the GRN, the accounts department will update the store’s ledger account.
Process of GRN
The following is the process of GRN:
- Receiving the invoice and challan and unloading of the goods to the stores.
- The physical verification of the number of goods received and the description of the goods.
- If the goods are disputed or are of a short quantity, the supplier is contacted asking for the shortfall.
- After the quantity is checked, the quality test is made.
- An acknowledgement shall be made by challan and sent to the supplier.
- After the above step, the receiving department will prepare the GRN in 5 copies. Original for them, and the remaining to the purchasing dept., accounts dept., one to the store manager, and one to the person making the purchase requisition.
- Based on it, entries are made to store ledgers.
Quality Inspection and GRNs
- Quality inspection and Goods Receipt Notes (GRNs) play pivotal roles in supply chain management and inventory control. Quality inspection is the process of meticulously examining products or materials to ensure they meet predefined quality standards.
- It is a critical step in preventing defective or subpar items from entering the inventory. Upon successful quality inspection, a Goods Receipt Note (GRN) is generated. A GRN is a formal document that serves as a record of the goods received in a warehouse or facility.
- It includes essential details such as the quantity received, supplier information, and item specifications. The GRN acts as a bridge between the procurement department and the warehouse, facilitating efficient inventory management. Quality inspection and GRNs contribute to the overall efficiency and reliability of the supply chain. By identifying and addressing quality issues early in the process, businesses can minimize the risk of disruptions, customer complaints, and costly returns.
- Furthermore, GRNs provide transparency, helping organizations keep accurate records of inventory levels, monitor supplier performance, and manage financial transactions effectively.
Conclusion
In conclusion, the Goods Received Note (GRN) is a pivotal document in the world of supply chain management and inventory control. It serves as a critical link between suppliers and businesses, providing a transparent record of goods received, their quantity, quality, and condition. Here are the key takeaways:
FAQs About GRN
The primary purpose of a GRN is to provide a formal record of the goods received, including details such as quantity, quality, condition, and compliance with purchase orders.
A GRN typically includes details such as the supplier’s information, the receiver’s information, a unique GRN number, date of receipt, purchase order number, item descriptions, quantity received, quality inspection results, and any remarks or comments.
A Purchase Order (PO) is a document issued by the buyer to request goods from a supplier, outlining the terms and conditions of the purchase. A GRN is created by the receiver to confirm the receipt of goods, comparing them to the details specified in the PO.
While not always mandatory, GRNs are highly recommended for maintaining accurate inventory records, verifying the quality of received goods, and resolving disputes or discrepancies with suppliers.
Related posts:
- AMC Full Form: Benefits, Components, Needs, Advantage
- ORS Full Form: Dehydration, Myths, Flavors, Varieties & Facts
- PCC Full Form: Importance, Types, Application Process
- PAN Full Form: Legal Provisions, Regulations,
- BRB Full Form: Productive, Routine, Distractions
- MCD Full From: Introduction, Responsibility, Challenges
- CT Scan Full Form: Scans, price, Advantages
- USA Full Form: History, Economics,Technology, culture