Fibre-reinforced plastic (FRP), also known as fiber-reinforced polymer (FRP), is a composite material made of a polymer matrix reinforced with fibers. The fibers are usually glass (in fiberglass), carbon (in carbon-fiber-reinforced polymer), aramid, or basalt. Rarely, other fibers such as paper, wood, boron, or asbestos have been used. The polymer is usually an epoxy, vinyl ester, or polyester thermosetting plastic, though phenol formaldehyde resins are still in use. FRPs are commonly used in the aerospace, automotive, marine, and construction industries.
- Introduction: FRP full form
- Types of Fibres Used in FRP: FRP full form
- Properties of FRP: FRP full form
- Manufacturing Processes: FRP full form
- Advantages and Disadvantages: FRP full form
- Applications of FRP: FRP full form
- Design Considerations for FRP Structures
- Process Description
- Material Requirement
- Conclusion
- FAQs
Introduction : FRP full form
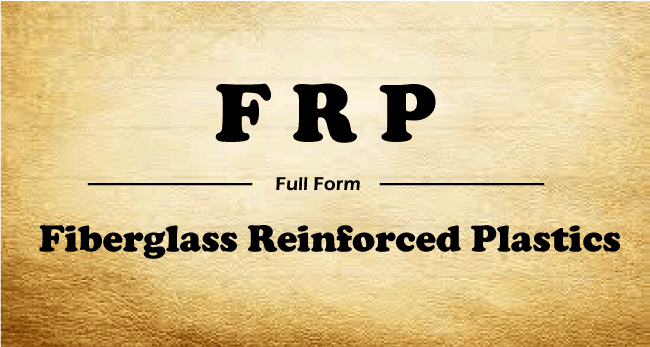
Definition of Fibre-Reinforced Plastic (FRP)
Fibre-Reinforced Plastic (FRP) is a remarkable composite material formed by combining a polymer matrix and reinforcing fibers. The polymer matrix, typically made of materials like epoxy, polyester, or vinyl ester, acts as a supporting structure. Reinforcing fibers, such as glass, carbon, aramid, or basalt, are embedded within the matrix to enhance strength, stiffness, and various other mechanical and physical properties.
Historical Background
The roots of FRP can be traced back to ancient times when natural fibers and resins were combined to create basic composite materials. However, the modern era of FRP began in the mid-20th century, marked by significant advancements in polymer technology and fiber manufacturing. During World War II, FRP gained prominence due to its use in various military applications. Since then, continuous research and technological development have evolved FRP into a versatile and widely adopted material across industries.
Importance and Applications
The importance of FRP stems from its unique combination of properties, including high strength-to-weight ratio, corrosion resistance, durability, and design flexibility. This makes FRP a preferred choice in diverse applications across several sectors, including but not limited to:
- Construction and Infrastructure: FRP is utilized in constructing bridges, buildings, and other structures, offering durability and resistance to harsh environmental conditions.
- Transportation: It finds applications in automotive, aerospace, and marine industries due to its lightweight nature, contributing to fuel efficiency and enhanced performance.
- Energy Sector: FRP is used in renewable energy infrastructure, such as wind turbine blades and solar panels, due to its strength and corrosion resistance.
- Sports and Leisure: In sporting equipment, FRP is employed to create lightweight and durable products like bicycles, golf clubs, and watercraft.
Types of Fibres Used in FRP: FRP full form
Fiber Type | Description |
---|---|
Glass Fibers | Common, strong, and cost-effective. They are like the workhorses of FRP, the regular heroes you often see. |
Carbon Fibers | Super strong, lightweight, and often used in high-tech applications like spacecraft and high-end sports gear. |
Aramid Fibers | Extremely tough, lightweight, and used in critical applications where strength is crucial, like secret agents. |
Basalt Fibers | Heat-resistant and capable of handling high temperatures, making them ideal for hot environments and car parts. |
Natural Fibers | Eco-friendly, lightweight, and derived from plants. They are like the heroes who love nature and are good for the environment. |
Synthetic Fibers | Man-made, versatile, and customizable to specific needs. They possess adaptable powers, much like versatile heroes. |
Properties of FRP: FRP full form
- Super Strong but Light: Imagine it’s as strong as a superhero, but as light as a feather. FRP is tough and can handle a lot of pressure, yet it’s not heavy like metal. This makes it great for things that need strength but shouldn’t be too heavy.
- Flexible and Bendy: It’s like a gymnast—it can bend and flex without breaking. FRP can handle being twisted or bent without losing its strength. This flexibility is handy in various applications.
- Resistant to Nasty Stuff: FRP is like a shield against chemicals and bad weather. It doesn’t get harmed easily by chemicals, water, or even extreme temperatures. It’s a tough protector!
- Lasts a Long Time: FRP is like the “Energizer Bunny” of materials—it keeps going and going! It lasts a really long time without wearing out, which is fantastic for things that need to stay strong for years.
- Custom-Made for Jobs: It’s like having a special tool for every task. FRP can be designed in different ways to suit specific jobs. Need it to be extra strong or look a certain way? FRP can do that!
- Looks Good, Too: FRP is like a fashion icon—it can look sleek and stylish. You can shape it into cool designs and colors, making it visually appealing for various uses.
Manufacturing Processes: FRP full form
- Mixing the Ingredients: Imagine baking a cake! In making FRP, we start by mixing the ‘ingredients’. We blend the plastic (like mixing flour) with the fibers (like adding chocolate chips) in the right amounts.
- Creating the Base: Just like spreading cake batter in a pan, we spread this mixture into the shape we want. It’s like molding clay into the shape you desire. This creates the base of our FRP.
- Baking or Curing: Now, it’s time to ‘bake’ our FRP. We put it in an oven-like space where it hardens and sets, just like baking a cake in an oven. This is called curing, and it makes the mixture solid and strong.
- Shaping and Polishing: Once it’s baked and cooled, it’s like taking the cake out of the oven. We can now shape and polish the FRP, just like decorating a cake with frosting. This step gives it a smooth and finished look.
- Quality Check: We then do a ‘taste test’, but not literally! We check the FRP for quality—making sure it’s strong, durable, and looks good. If it passes the test, it’s ready to be used in various cool things!
Advantages and Disadvantages: FRP full form
Advantages
- Lightweight and High Strength: FRP is like a superhero—it’s really strong but not heavy. This makes it perfect for things that need strength without being cumbersome.
- Corrosion Resistance: FRP acts like a shield against rust and other damage caused by chemicals or bad weather. It can last longer without corroding.
- Design Flexibility: It’s like a chameleon—it can take different shapes easily. FRP can be molded into various forms, making it highly adaptable to different designs.
- Excellent Chemical Resistance: FRP is like a warrior against chemical attacks. It can withstand exposure to many harsh chemicals without getting harmed.
- Durable and Long-lasting: It’s tough and sturdy, like a well-built fortress. FRP can endure a lot of wear and tear, making it last for a really long time.
- Electrical Insulation: FRP acts like an electrical guard. It doesn’t conduct electricity, making it safe to use in electrical applications.
- Low Maintenance: Like a low-maintenance pet, FRP doesn’t need a lot of attention. Once installed, it generally requires minimal upkeep.
Disadvantages
- Cost: Initially, it can be a bit pricey to use FRP compared to some other materials.
- Brittleness: Sometimes it can be a bit fragile and break easily under extreme conditions or impacts.
- Environmental Impact: The process of making FRP might not be very environmentally friendly in some cases.
- Temperature Sensitivity: It can change shape or warp if exposed to high temperatures for a prolonged period.
- UV Degradation: Prolonged exposure to sunlight can weaken the material over time.
- Limited Repair: If it gets damaged, it’s not always easy to fix. Repairing FRP can be a challenge compared to other materials.
Applications of FRP: FRP full form
Application Area | Description |
---|---|
Construction and Infrastructure | Bridges, buildings, roofing, cladding, reinforcement bars, and panels for their durability, strength, and corrosion resistance. |
Transportation | Automotive components, aircraft parts, boat hulls, railcar components due to their lightweight, high strength, and durability. |
Energy Sector | Wind turbine blades, solar panel supports, transmission poles, and oil and gas industry equipment for their corrosion resistance and durability. |
Marine and Boating | Boat hulls, decks, and other components due to their resistance to water, salt, and UV exposure while maintaining strength and lightweight properties. |
Sports and Recreation | Bicycles, kayaks, snowboards, helmets, and sports equipment for their lightweight, strength, and flexibility, enhancing performance. |
Industrial Equipment | Chemical storage tanks, pipes, and ducts due to their corrosion resistance, lightweight, and ease of installation and maintenance. |
Aerospace | Aircraft components like wings, fuselage, and interior structures due to their high strength-to-weight ratio, enhancing fuel efficiency and performance. |
Design Considerations for FRP Structures
Designing with FRP is like building with Lego blocks – you need to consider a few important things to make sure everything fits together just right!
- Choosing the Right Fiber: It’s like picking the right type of material for your Lego project. Depending on what you’re building, you need to choose the appropriate fiber (like glass, carbon, or aramid) that suits the strength and purpose of your structure.
- Understanding the Environment: Just as you’d consider where to build your Lego creation – indoors or outdoors – you need to think about where your FRP structure will be. Different environments can affect FRP differently, so plan accordingly.
- Designing for Loads: Like making sure your Lego tower can hold up the weight of the top blocks, in FRP design, you need to calculate and plan for the loads (forces and pressures) your structure will experience. This ensures it stays strong and safe.
- Ensuring Durability: FRP is like a tough Lego piece, but you still need to think about how long it’ll last. You want your creation to endure, so design with materials and techniques that ensure durability against wear, tear, and other stresses.
- Considering Joints and Connections: Just as you need to fit Lego pieces together securely, in FRP design, you have to think about how different parts of your structure will connect. The joints need to be strong and well-designed to maintain the overall strength of the structure.
- Adapting to Manufacturing Processes: It’s like understanding which Lego pieces you have available for your project. Design with the manufacturing process in mind – whether it’s pultrusion, molding, or another technique – to ensure a seamless construction process.
- Thinking About Maintenance: Consider how easy it will be to take apart and reassemble your Lego creation. Similarly, design FRP structures with maintenance in mind, ensuring accessibility and ease of future repairs or modifications.
Process Description
Material Selection: The manner of manufacturing fibre-reinforced plastic (FRP) starts with cautious choice of substances tailored to meet the favored characteristics of the final product. This includes choosing the proper polymer matrix, which include epoxy, polyester, or vinyl ester resin, and selecting the type and configuration of reinforcing fibers, that may consist of alternatives like glass, carbon, aramid, or basalt fibers.
Preparation of Reinforcement: Before incorporation into the polymer matrix, the reinforcing fibers undergo preparation steps to decorate their compatibility and adhesion with the resin. This may contain remedies which includes sizing or surface adjustments to promote bonding between the fibers and the matrix material.
Mould Preparation: A mildew is ready based at the favored form and dimensions of the very last FRP product. The mildew can be made from various substances, including metals, fiberglass, or composite materials, and is designed to facilitate the shaping and curing of the composite fabric.
Lay-up: In this step, the organized reinforcing fibers are cautiously organized inside the mold in line with the favored orientation and configuration. This can be performed manually by way of layering pre-reduce fiber sheets or the use of automatic methods together with filament winding or automated tape laying to attain unique fiber placement.
Resin Infusion or Impregnation: The polymer matrix, normally in liquid form, is implemented to the reinforcing fibers to saturate them and fill the voids among the fibers. This can be completed thru techniques together with hand lay-up, vacuum infusion, resin transfer molding (RTM), or pultrusion, ensuring uniform distribution of the resin at some stage in the composite shape.
Material Requirement
Polymer Matrix: The choice of polymer matrix is essential because it determines many properties of the FRP, consisting of mechanical strength, chemical resistance, and temperature stability. Commonly used matrices consist of epoxy, polyester, vinyl ester, and thermoplastic resins. The choice relies upon on elements including fee, processability, and overall performance requirements.
Reinforcing Fibers: The sort of reinforcing fibers selected considerably affects the mechanical homes of the FRP, together with tensile power, stiffness, and impact resistance. Common reinforcing fibers encompass glass, carbon, aramid, and basalt fibers. The preference depends on factors consisting of power-to-weight ratio, cost, and environmental situations.
Resin System: The resin device performs a vital role in bonding the reinforcing fibers collectively and supplying protection towards environmental factors such as moisture and chemicals. Factors to do not forget while choosing a resin device encompass compatibility with the reinforcing fibers, curing traits, and resistance to particular environmental conditions.
Fillers and Additives: Fillers and components can be integrated into the resin device to modify houses consisting of viscosity, thermal conductivity, flame resistance, and UV stability. Common fillers consist of calcium carbonate, silica, and talc, even as additives may additionally consist of UV stabilizers, flame retardants, and processing aids.
Mould Materials: Mould substances have to own dimensional stability, floor finish, and durability to resist repeated use at some stage in the producing system. Common mildew materials consist of metals (inclusive of aluminum and metal), fiberglass, and composite materials. The preference depends on elements together with cost, complexity of the part geometry, and required surface end.
Conclusion
Fibre-Reinforced Plastic (FRP) is a true marvel of modern engineering, embodying strength, versatility, and innovation. By combining polymers and reinforcing fibers, FRP exhibits extraordinary properties that have revolutionized various industries.
A Material of Remarkable Strength and Lightness: FRP possesses the incredible ability to be lightweight while maintaining exceptional strength. It’s like having the strength of steel but without the heaviness. This characteristic makes it ideal for a wide range of applications, from aerospace to everyday consumer products.
Flexibility and Adaptability in Design: Much like a chameleon adapting to its surroundings, FRP offers immense design flexibility. Its adaptability allows for the creation of complex and intricate shapes, meeting specific project requirements with ease. Architects, engineers, and designers cherish FRP for its ability to turn creative visions into reality.
FAQs
Q1:What is FRP used for?
A: FRP is used in construction, aerospace, automotive, marine, and industrial applications for lightweight, strong, and corrosion-resistant components.
Q2: What does FRP mean?
A: FRP stands for Fibre-Reinforced Plastic, a composite material consisting of a polymer matrix reinforced with fibres to enhance strength and durability.
Q3:What is the full form of FRP in corporate?
A: FRP often stands for Financial Restructuring Plan. This refers to a strategy implemented by a company to reorganize its financial structure, typically to improve financial stability, manage debt, or address financial distress
Q4:What is the full form of FRP in corporate?
A: In a corporate context, FRP commonly stands for Fixed-Rate Pension
Q5:Is FRP material good or bad?
A: FRP (Fibre-Reinforced Plastic) material has both advantages and disadvantages, making it suitable for some applications while less ideal for others.